REVOLUTION IN AEROSPACE MANUFACTURING WITH 3D PRINTD SEALANTS
Jim Cairns
PPG
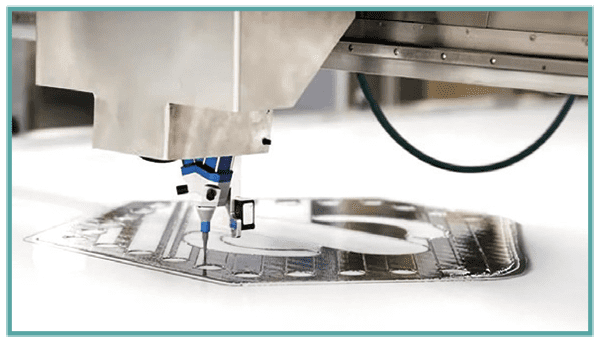
The Aerospace sector continues to develop and adopt new advanced materials such as carbon fiber based composite materials, titanium, high-performance ceramic materials, and various metal alloys. Manufacturing processes, therefore, constantly evolving nowadays, represent an increasingly important challenge for material producers which must combine efficiency and precision.
PPG offers a complete range of innovative products for Original Equipment Manufacturers (OEMs) involved in both commercial and military aviation sectors. For the Aerospace sector, PPG’s Ambient Reactive Extrusion (ARE) technology aligns with this ongoing transformation, offering high-efficiency PPG ARETM 3D extruded sealants that improve operational efficiency and redefine the sealant application methods, while also reducing costs (estimated around 30%) and material waste.
This new sealant application method represents a breakthrough for the sector because they are an exceptional example of how innovation and production evolution come together to maximize manufacturing processes.
These preformed PPG ARETM 3D printed sealants eliminate the need for manual sealant molding and can be printed and shipped on demand once developed. Thanks to the development of this innovative process that preforms the sealants, users improve the application on various components. 3D printing technology produces uniform, consistent, and dimensionally accurate parts. This precision helps ensure that applications meet the highest performance and safety standards for the components and structural parts being produced. The new PPG ARETM 3D printed sealants have been designed for a wide range of aerospace applications, making them the ideal choice for various projects such as fuel tanks, wing seals, doors and windows, thermal barriers protecting components from thermal fluctuations, and custom closures with unique bonding requirements.
Jim Cairns, PPG’s Additive Manufacturing Director for aerospace coatings and sealants adds more details about the technology.
In an industry such as Aerospace where high- performance materials are used, what is the main advantage of using these 3D printed sealants?
“At PPG, we see four main advantages to using PPG ARETM 3D printed sealants. The first advantage is higher accuracy since the part is the same every time. There are no significant variances as it takes the variability of hand applied sealants out of the picture. Second, in almost all instances, it is a faster application process. This eliminates much of the application time as well as time waiting for sealants to cure before the next step in the process. It can eliminate bottlenecks. Third, 3D printed sealants contribute to sustainability. Rather than using and disposing of many cartridge kits, only a few are used. Finally, the preformed sealants have an extended shelf life and do not ship as hazardous chemicals, easing supply chains”.
In addition to Aerospace, which sector is increasingly demanding the use of these sealants developed by PPG?
“In 2021, PPG began using the 3D printing technology in its Aerospace business since the technology is an excellent fit for this industry. We currently have more than 60 projects in process with airline manufacturing and maintenance companies. We will continue our efforts to expand into other markets like industrial coatings, railcar and several other specialty markets”.
Can you explain why these sealants could lead to a ‘revolution’ in the manufacturing process across the industrial sectors?
“PPG ARETM 3D printed sealants also have the potential to solve other industrial sealant situations. Any application that requires attributes like high chemical resistance, high temperatures, exacting fitment requirements, long shelf life or difficult applications can benefit from PPG ARE™ 3D printed sealants. The technology is very new and the potential applications are enormous”.