Bio-based adhesive systems for PVC floor coverings using biological principles from nature
Lorenzo Tomei
FRAUNHOFER IVV
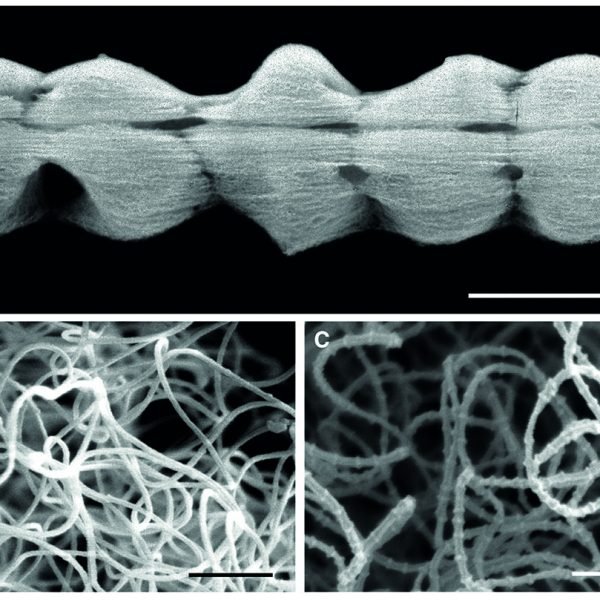
Industrial adhesives are used in a variety of different situations and are therefore subject to a very broad requirement profile, ranging from extremely high bonding strength to being easy to detach. Adhesives that combine both properties are very difficult to develop. As a result, development focuses primarily on ensuring bonding strength, making it difficult to detach and remove bonded components. This is the case for floor coverings such as PVC, for example, which are often very difficult to remove properly.
At the same time, most adhesives nowadays are made from petroleum-based polymers, which release highly volatile, strong-smelling substances that can be hazardous to human health. This means that many costintensive measures need to be put in place throughout the value chain, from extraction to disposal, in order to protect people and the environment.
The KleBoSpin project has developed adhesive systems for elastic floor coverings (such as PVC) that provide a bonding strength high enough to meet the requirements placed on them. The added value of the bio-based floor adhesives is that the floor coverings can easily be detached and removed. With this project, Fraunhofer IVV is looking to take the principle used by spiders to catch prey and transfer it to adhesive systems for floor coverings. The development work is aimed at creating an adhesive system that provides adequate bonding strength while being easier to detach when removing floor coverings. Unlike conventional adhesives, the product will also be free from formaldehyde and any substances that are harmful to human health, meaning that no cumbersome or cost-intensive occupational health and safety measures are required during manufacturing, use and disposal.
Lorenzo Tomei explains the project and the inspiration from which the new adhesive development is born.
The Klebospin project is developing adhesive systems for elastic floor coverings. Whati is the biggest challenge to face in the field of adhesive formulations?
Tomei: “In our research project ‘KleBoSpin’, we researched an adhesive system that was completely based on raw materials of natural origin and, specifically, completely from plant biomass.
The development was directed toward an adhesive system for elastic floor coverings.
The great, but at the same time stimulating challenge was not only to obtain a completely bio-based system that would ensure sufficient adhesion for such an application. In fact, our idea was also to create an adhesive that would allow the flooring to be removed easily enough so that it could eventually be recycled for subsequent applications.
Therefore, our aim was to find a sustainable solution from the point of view of choosing natural, non-toxic materials that are not derived from fossil resources, but from renewable plant biomass, and at the same time that kept in mind the sustainability aspect of the life cycle and the reuse of widely used materials such as PVC for floorings.
Balancing all these aspects when choosing the materials and formulating them was a path that required several iterations, a good knowledge from Fraunhofer IVV of the techno-functional properties of biogenic materials for technical applications, and, of course, a fair amount of creativity!”.
TIn an adhesive, the most important component is the plymer, how can we develop a bio-based polymer that is equivalent in performance to traditional ones?
“To have a performing adhesive, surely the first place to start is a polymer with excellent functionality as a binder. Although some drop-in solutions already exist, such as epoxy polymers obtained from biological sources and with chemical structures similar to their petrochemical counterparts, we preferred to approach the problem from another perspective and try to find an out-of-thebox solution. Instead of focusing all our efforts on trying to imitate conventional polymers and obtain them from renewable plant sources, we thought, why not look for an effective solution that is already present in nature and try to imitate its physical principle for our purpose of interest?
And so that is how the KleBoSpin project (from the German Klebstoff = adhesive, Bodenbelag = flooring, and Spinne = spider) was born precisely to try to answer this question”.
What natural resource are you exploiting to formate the adhesive?
“To develop our adhesive system, we were indeed inspired by the marvelous example of spider webs, as hinted earlier by the project name. Nature itself is already an endless goldmine of ingenious and efficient ideas. Spiders, in fact, make the best use of their webs to catch their prey, which, once in contact with the web, remain attached to it and the spider can then enjoy its meal. A very interesting fact is that some spiders, known as cribellates, do not use any adhesive substance to make their webs into sticky traps, but make simple and ingenious use of the natural wax that covers the cuticle of their prey. In fact, many insects dispose of an external wax layer to prevent their limbs from over-drying. When these insects come in contact with the spider web, their cuticular wax begins to penetrate by capillarity and electrostatic forces into a very dense network of pores, which results from the web’s filamentous structure. In fact, the cribellate spiders are capable of spinning complex fibrous structures, consisting of two axial fibers that serve as the supporting structure and thousands of nano-fibers with a diameter of 20-30 nm consisting of a special fibrous protein, the socalled fibroin. This myriad of nano-fibers forms a woolly cloud around the two axial fibers that has an incredibly large specific surface area because of its nanometer size.
This immense surface area is the reason why capillary and electrostatic forces enable the absorption of the cuticular wax of the prey and ensure its adhesion on the web. And it is precisely this physical principle that occurs at the nanoscale that we have tried to imitate and recreate on a larger scale as well”.
Some manufacturers look at the behavior of mussels to develop adhesives. What inspired you for you profect?
“First, to mimic and recreate the porous nanostructure of cribellate spider webs, we went looking for a solution by combining proteins and carbohydrates. Due to our decades of experience in proteins for technical applications, we already had it clear in our minds that to achieve a porous structure we could rely on the excellent ability of plant proteins to incorporate air and stabilize it in the form of foams. We all have some experience of this, after all: just think how albumin, the main protein in egg whites, is able to form incredibly stable foams when eggs are beaten stiff. The next step we needed was to figure out how we could stabilize these highly aerated structures in a stable material that can tolerate the compressive stresses of an elastic floor covering. And that is where cellulose and its derivatives come into play. Cellulose, the most available biopolymer on the earth’s surface and the structural element of plant cell walls, was the perfect solution to reinforce such a foamy structure. Through several iterations, different mixing ratios and multiple formulations of protein, cellulose and cellulose derivatives, we arrived at a porous yet stable structure that could be adapted for a flexible flooring.
What was still missing was how to recreate the cuticular wax of insects, though. And here the answer came from the great diversity made available by plant waxes, such as carnauba wax or candelilla wax, which are often used to polish shoes or even cars. Through a process of emulsification, we obtained vegetable wax formulations that could have a viscosity such that they could both be spread easily on a screed and quickly penetrate the porous structure previously described. The choice of wax type was also dictated by the possibility of being able to easily remove the flooring by heating and consequently reducing the viscosity of the wax and, therefore, the adhesion.
Through these three simple classes of natural ingredients, we were able to produce a prototype A4 adhesive system that validated our idea and the working principle of spider web on a larger scale as well”.
Has Fraunhofer already been supported by manufacturing companies that want to invest in the project to differentiate their production?
“The purpose of our project was first to demonstrate that the natural principle also worked outside its natural environment and that it could also be reproduced on a larger scale. In that sense this was possible.
However, several questions remain for a concrete translation of our idea into an actual product. What would still be interesting to investigate is, for example, whether our adhesive system is compatible with all types of elastic floorings and screeds, how the adhesive properties vary under different ambient humidity and temperature conditions, under what conditions the formulations can be stored and how long, how to scale up the production of the formulations. As Fraunhofer IVV is an applied research institute, the challenge of finding solutions that have practical utility and can be used tomorrow by a company is what stimulates us and drives us to always come up with new ideas. Therefore, we are more than open to companies that are interested in pursuing the idea generated and tested in the “KleBoSpin” project and collaborating to take the developed technology one step further”.